UNIST, KAI와 손잡고 항공기용 복합재 부품 만든다!
2019.10.07UNIST, KAI와 손잡고 항공기용 복합재 부품 만든다!
박영빈, 지우석 교수팀 차세대 대형 민항기용 부품 제작 위한 산자부 과제 선정
5년간 100억원 연구비 투입 … 생산성 높이고, 소재 재활용 앞당길 기술 개발
2019.09.24김 석민대외협력팀
가볍고 튼튼한 복합재는 항공기의 주요 부품 생산을 위한 핵심 소재다. 이 항공기용 복합재 부품을 더욱 간단하고 저렴하게, 또 친환경적으로 만들기 위한 연구가 UNIST에서 시작된다.
박영빈, 지우석 기계항공 및 원자력공학부 교수팀이 국내 최대 항공기 제작업체인 ‘한국항공우주산업(KAI)’과 함께 차세대 대형 민항기용 부품 제작 과제에 선정됐다. 이번 연구과제는 산업통상자원부에서 추진하는 항공부품산업 공정기술개발사업의 일환으로, 2019년 7월부터 5년간 총 연구비 100억 원이 투입된다.
연구주제는 ‘단일 통로 민항기용 4미터 이상급 복합재 주익 일체형 모듈 및 3미터 이상급 열가소성 복합재 동체 모듈 개발’이다. 연구진은 기존 복합재 생산을 위한 소재와 공정의 비효율성을 개선하면서도 고품질의 복합재 부품을 생산하기 위한 기술개발에 나선다.
현재의 항공기 복합재는 재활용이 불가능한 열경화성 수지를 재료로 제작된다. 열경화성 수지를 성형하기 위해서는 높은 열과 압력이 필요한데, 여기에 사용되는 장비가 ‘오토클레이브(Autoclave)’다. 항공기에 적용되는 대형 부품을 제작하기 위해서는 대형 오토클레이브가 필요한데, 이러한 장비는 구축비용도 많이 들뿐더러 수지경화에도 평균 10시간 이상이 소요된다.
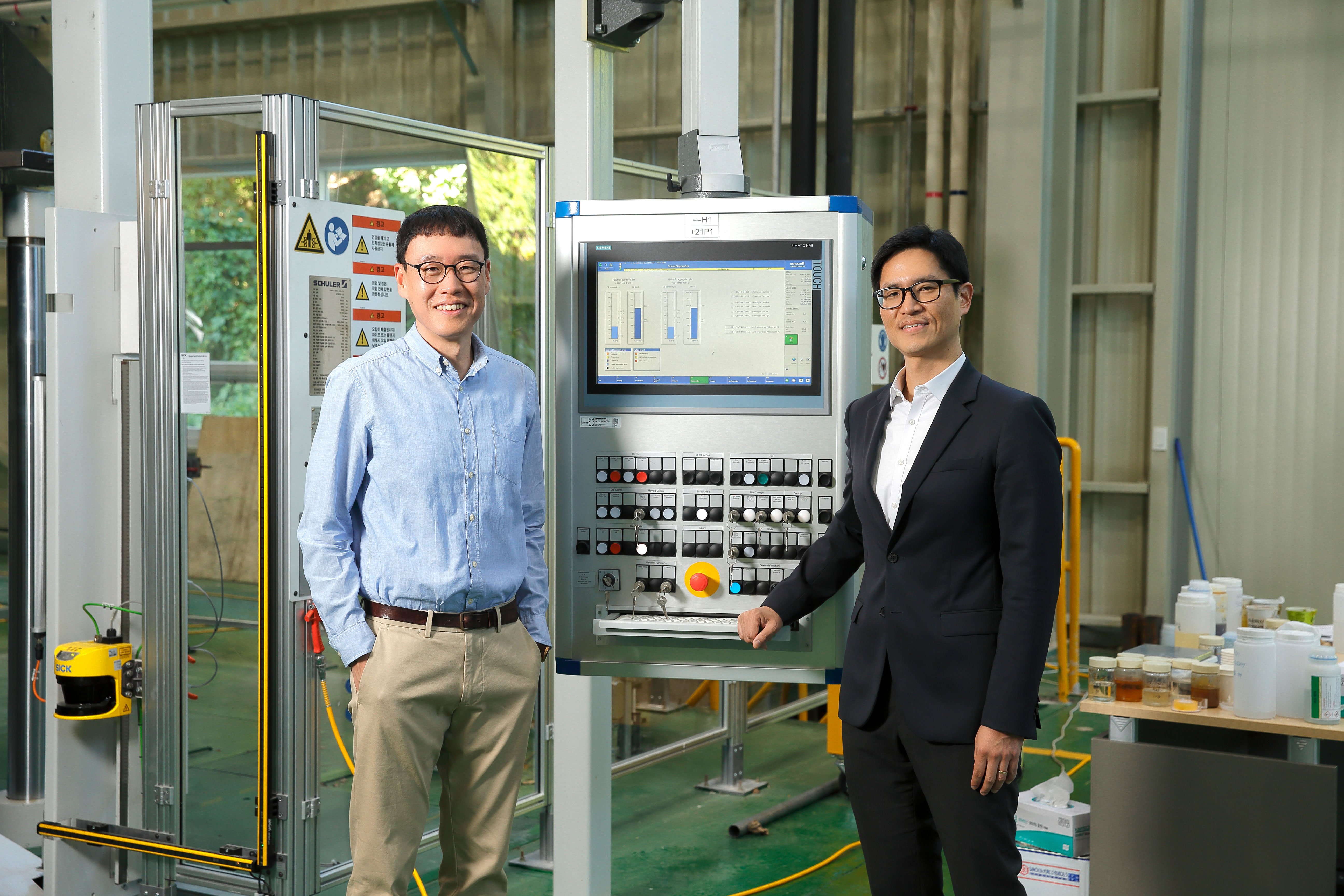
지우석 교수는 “열경화성 수지는 재활용이 안 된다는 점에서, 대형 오토클레이브는 생산성이 낮다는 점에서 현재의 복합재 성형공정은 명확한 한계를 갖고 있다”며 “이번 연구 과제는 기존의 소재와 공법을 버리고 혁신적인 친환경 소재와 생산성을 확보하는 것을 목표로 한다”고 강조했다.
연구진은 열을 가하면 재활용할 수 있는 열가소성 수지를 이용해 수 분 내로 부품을 제작할 수 있는 성형법 개발에 나선다. 특히 이번 과제는 기초기술 개발은 물론 실제 제품제작까지 그 범위가 넓다. 기술개발에 그치지 않고, 제품 제작공정까지 함께한다는 점에서 타 과제에 비해 대학의 역할이 큰 편이다.
이처럼 기업과 대학이 함께 사업화를 목표로 하는 프로젝트가 성사될 수 있었던 데는 UNIST 내에 구축된 복합재료기술 연구센터(센터장 박영빈)의 역할이 컸다.
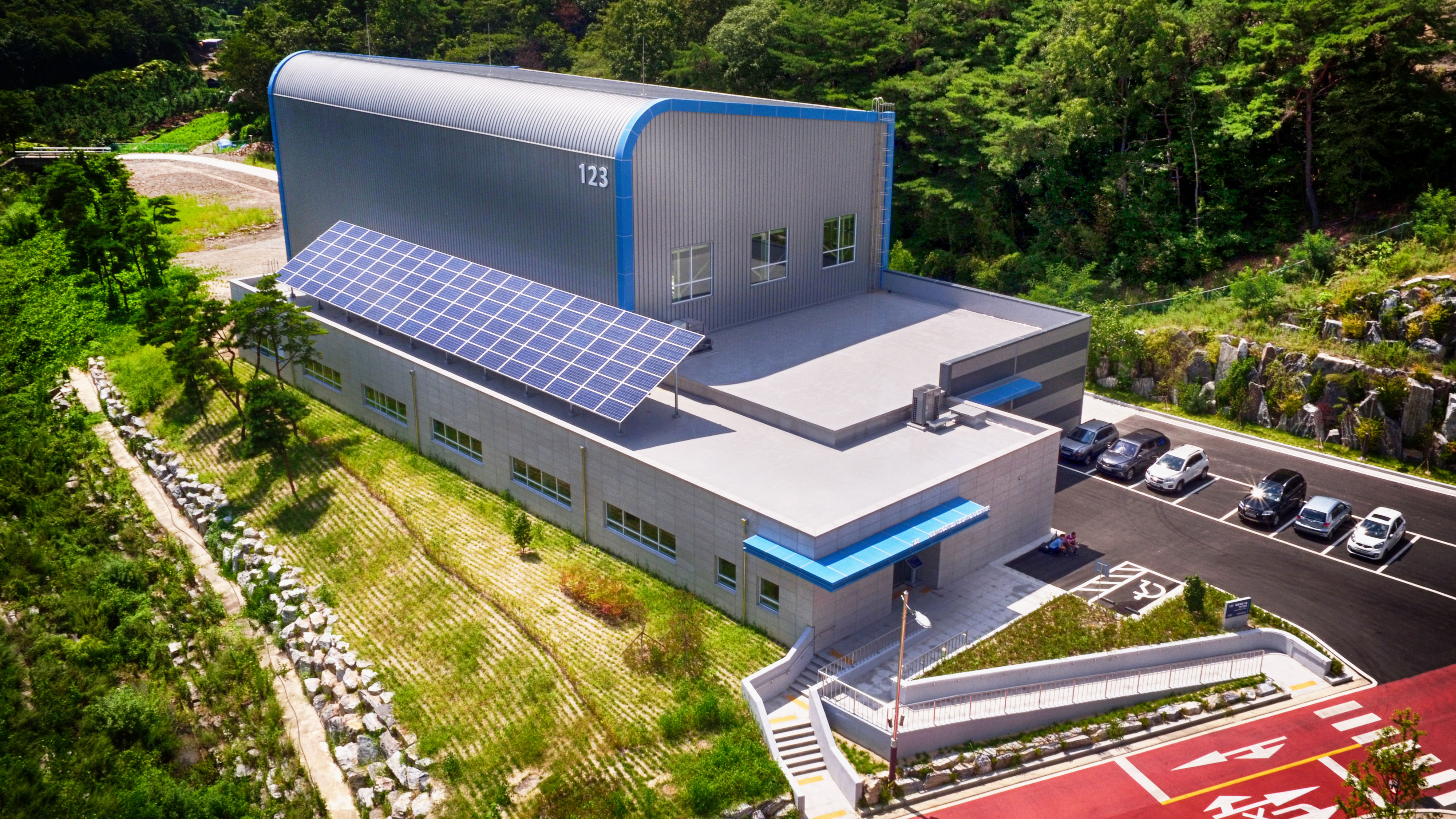
복합재 고속 성형 기술의 중요성을 일찌감치 깨달은 박영빈 교수는 꾸준히 연구기반 확보를 위해 노력해왔다. 그 결과 2016년 아시아 최초로 프라운호퍼 화학기술연구소의 분원을 유치했으며, 지난 2018년 11월 성공적으로 연구센터 준공식을 마쳤다. 123동에 마련된 복합재료기술 연구센터에는 100억 원 규모의 복합재 고속 성형 장비가 구축돼 운영 중이며, 성형, 소재, 해석 등 복합재 전 분야에 걸쳐 특화된 연구팀이 상주하고 있다.
박영빈 교수는 “최근 복합재 연구는 생산성을 높이는 노력과 함께 환경보존을 위한 재활용 방법을 확보하는 분야로 확장되고 있다”며 “이번 과제를 통해 개발하고자 하는 기술은 복합재 재단 후에 남은 스크랩이나 퇴역 항공기의 부품을 회수해 새로운 부품을 제조할 수 있는 기술로, 항공 산업 외에도 복합재가 활용되는 다른 산업에 적용할 수 있을 것”이라고 설명했다.